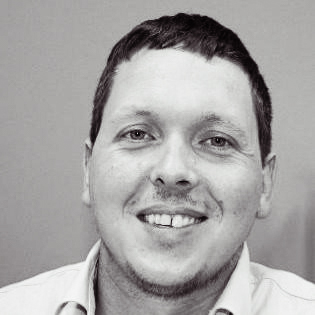
The curing of concrete is essential to developing the strength and durability of concrete. Curing prevents the concrete from drying prematurely, helps to maintain the concrete temperature and aids in the bonding of the concrete to internal materials. Properly cured concrete will be strong, possess volume stability, be resistant to freezing, thawing, abrasion and scaling. Concrete that isn’t cured properly can become brittle and flaky.
“Concrete never stops curing,” says Stuart Galloway, President, Canadian Concrete Expo. “It continually hardens for its entire life. Although, it does reach a point when changes become unnoticeable.”
The American Concrete Institute (ACI) Committee 301 recommends a curing period in which 70 percent of the specified compressive strength is attained. Many times, this can be achieved in seven days but factors such as mixture proportions, specified strength, the size and shape of the concrete member and ambient weather conditions, can influence the rate of curing.
In some instances, in order to attain the desired concrete properties curing is initiated prior to the finishing stage.
There are three stages to curing,” says Galloway. “In the first stage, initial curing, when the concrete is placed and compacted, the concrete bleeds water up to the surface and evaporates. Reducing the amount of bleeding is essential to eliminating plastic shrinkage. Intermediate curing is when done when concrete surface finishing operations, such as troweling are complete. Final curing conducted after the final setting of concrete helps to prevent surface drying.”
Precast plants are acutely aware of the effects of curing. Options for curing concrete include the following:
· Curing with warm air, moisturizing
· Curing with Turbostream
· Curing with warm water
“When choosing a curing solution, producers and plants should consider their final products,” says Juha Niemi, Sales Director, Polarmatic Oy, Tampere, Finnland. Polarmatic is a leading developer and supplier of heating, curing, cooling, control, and information management solutions specifically developed for the concrete industry.
Curing with Warm Air
Warm air curing is commonly used by producers of blocks, pavers, or other architectural precast products that must have uniform appearance. “Heated air circulates in the curing chamber or kiln,” says Niemi. “This gives even distribution of heat. When increasing the temperature of the curing chamber or kiln, you want to add a little moisture to keep the relative humidity on a high level to avoid drying out the product surface.”
Curing with Warm Water
Warm water is used by plants that produce products for the housing market, such as walls and ceilings; pre-stressed hollow core slabs; and concrete products produced with casting tables. In these applications, warm water is circulated below the molds and tables used to contain the fresh concrete.
Curing with Turbosteam
Turbosteam is commonly used for precast products used in infrastructure works, such as drainage piping, manholes, and other products that will be buried underground. With Turbosteam, combustion gas is combined with steam to provide a carbon dioxide rich, moist heating medium. “Products cured with Turbosteam are mostly dry-cast products, because the producers need the concrete surface to stay moist,” says Niemi. Because Turbosteam circulates carbon dioxide within the curing chambers, it also results in increased initial strength of the concrete and therefore allows faster curing times.
Notes:
1. This blog is courtesy of the Canadian Concrete Expo, Toronto, Jan. 22-23, 2020. For more, visit: https://canadianconcreteexpo.com/.